Design ⬩ Develop ⬩ Manufacture ⬩ Support ⬩ Train
From designing expectational composite products to manufacturing conforming components and providing high-quality aftersales support, we seamlessly integrate each of our industry-standard processes in industry-leading ways.
Our integrated product development process enables us to offer a broad range of design and specification, first part qualification and build-to-print solutions implemented to ensure you get the quality product as per your application requirements.
Our integrated product teams work in synergy to understand your unique composite manufacturing challenges and offer expert advice, based on decades of industrial experience in composites.
We develop novel materials & cutting-edge process technologies and use them in high-value and high-volume manufacturing to produce superior sustainable composite products.
We thrive by working on challenging assignments. The complexity of the project helps us deploy our expert engineering competence in diverse situations. We succeed in delivering where others can’t. That is what makes us one of the leading global supplier of engineering services and composite products, originating from India.
Our team’s expertise in advanced manufacturing has helped us produce anything from a uniquely designed one-off component to a series of customer-designed products, using the latest composite technology. We are able to offer bespoke training courses to empower aspirants wanting to work in Composite Industry.
Design and Engineering Capabilities
Datum’s experienced Product Design and Development team uses top-of-the-line globally recognised 3D design, engineering, simulation, project management and PLM tools, such as:
- Dassault Systèmes’ 3D Experience
- Autodesk AutoCAD
- MathWorks MATLAB
- Ansys
- MSC NASTRAN / PATRAN
- Microsoft Office 365 and Microsoft Project
More information on Design and Engineering service can be found here.
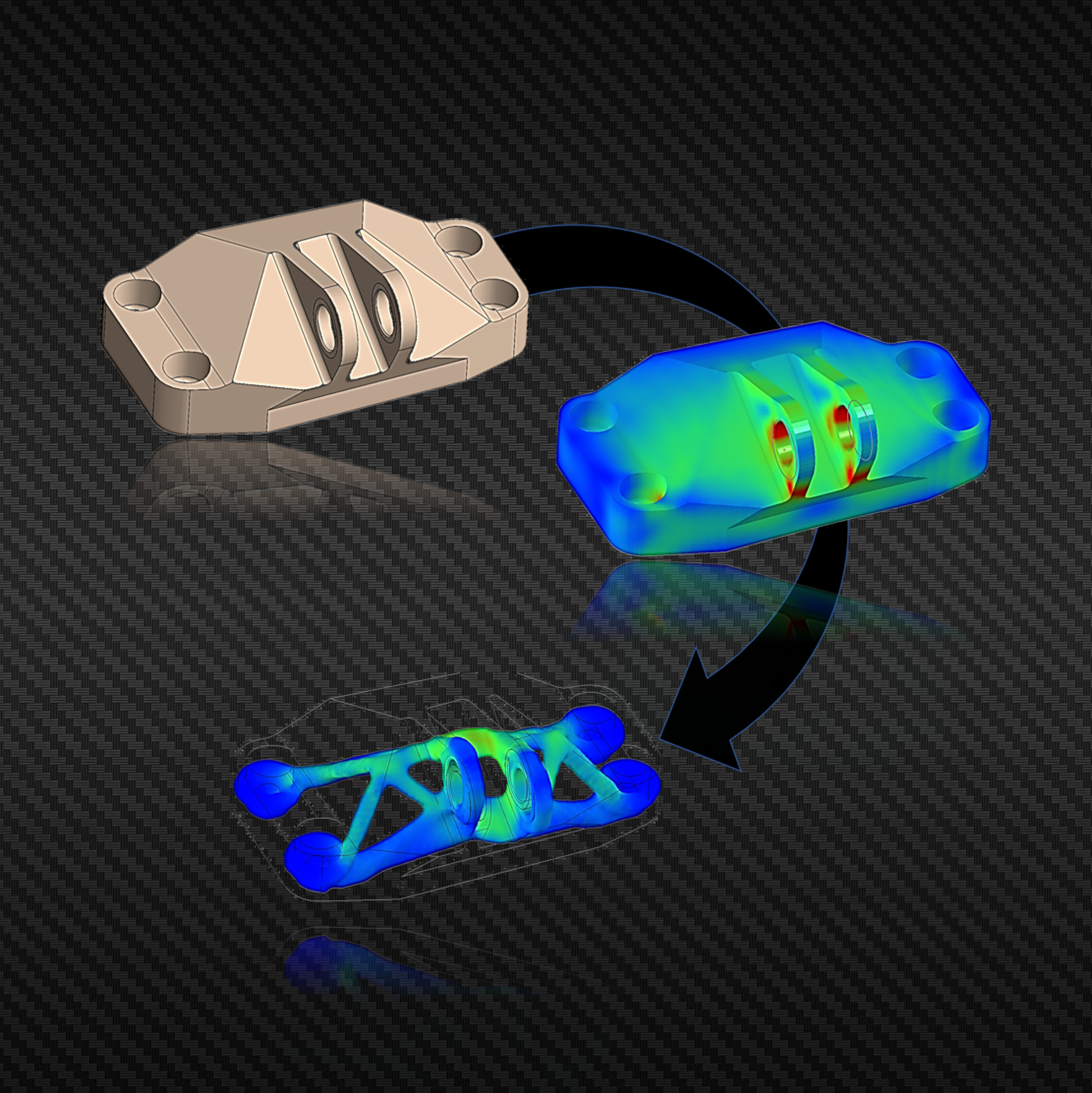
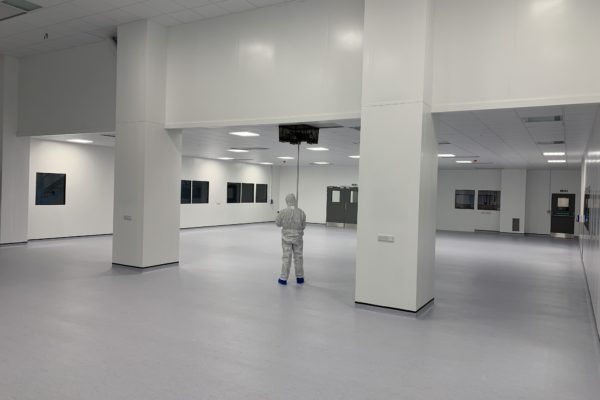
Composite Processing Capabilities
Datum’s state-of-the-art Advanced Manufacturing Facility houses various sophisticated equipment and technologies capable of fabricating zero-defect polymer composite structures, such as:
- Contamination Controlled Areas (CCA) – clean rooms that are equipped with automated controls and monitoring for temperature & humidity parameters. The areas are kept up to standards using principles of 5S.
- Variable flow rate and variable vacuum pressure pumps ideal for manual, liquid and prepreg composite moulding.
- Composite Curing Ovens that are fully-integrated and programmable using calibrated and reliable PID controllers and thermocouple data loggers.
More information on our Advanced Composite Manufacturing service can be found here.
Advanced Manufacturing Facility Shop Floor
Along with conventional composite processing capabilities, the Advanced Manufacturing Facility encompasses:
- Machine Shop – equipped with manual and numerical-controlled milling, drilling and turning machines, and other power tools.
- Paint Shop – contains spray and paint booths with in-situ curing capability in an environmentally monitored area.
- Inspection & NDT Cell – houses composite and metal inspection and non-destructive test equipment to ensure we supply zero-defect products.
More information on our manufacturing capabilities and related services can be found here.
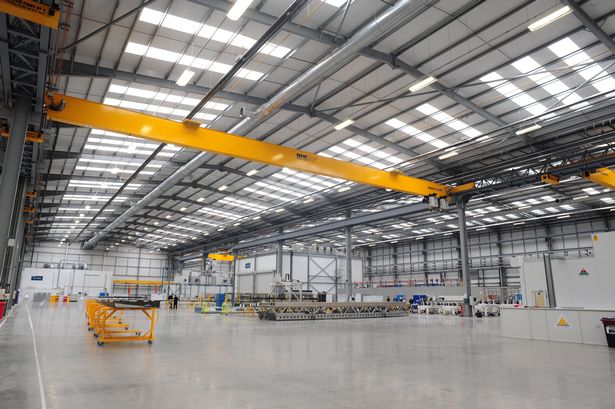
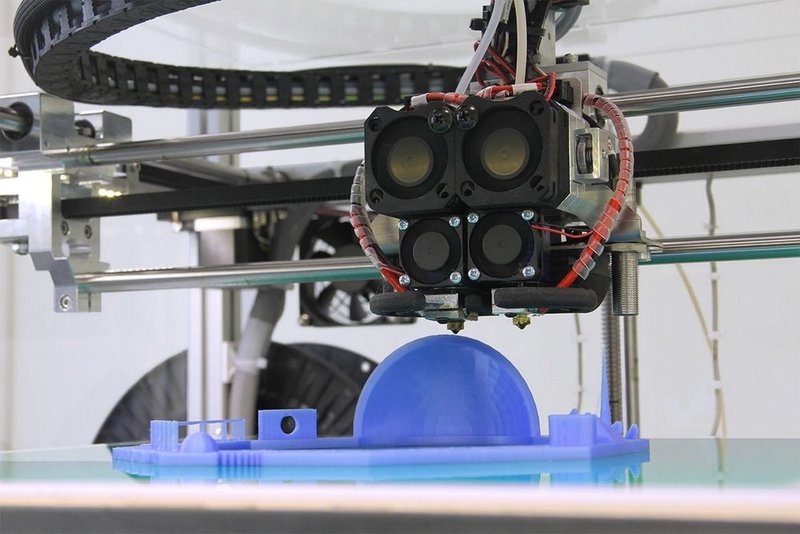
Additive Manufacturing Capabilities
From producing very complex geometrical prototypes to 3D printing bespoke composite tooling aids and load bearing structures, Datum boasts both Fused Filament Fabrication (FFF) / Fused Deposition Modelling (FDM), and Stereolithography (SL) capabilities.
We offer the following:
- Maximum Part Size: 300 x 300 x 600 mm
- Minimum Part Size: 10 x 10 x 10 mm
- Lead Times: From 1 Working Day
- Tolerance: ± 0.5% (min: ± 0.5 mm)
- Layer Height: 100 microns (where applicable)
- Minimum Wall Thickness: 1.0 mm
More information on our Additive Manufacturing service can be found here.
Material Characterisation & Product Evaluation Capabilities
Our Material and Process Development Facility is equipped with calibrated machines to boost material testing and product evaluation capabilities, including:
- Universal Testing Machine – measures key mechanical properties of composite materials and structures.
- Differential Scanning Calorimeter (DSC) – determines melting and curing characteristics of a polymer matrix for a composite.
- Dynamic Mechanical Analyser (DMA) – measures the change in the viscoelastic properties of a polymer with changing temperature.
- Electrical Resistance Tester – measures electrical conductivity of composites modified with special additives and nano-fillers.
- Microscope – analyses features like surface morphology and fracture surfaces, before and after testing or post-processing.
- Environmental Chamber – conditions composite test specimens under non-ambient conditions such as hot, wet, dry, cold, sub-zero, etc.
More information on our Material Characterisation service can be found here.
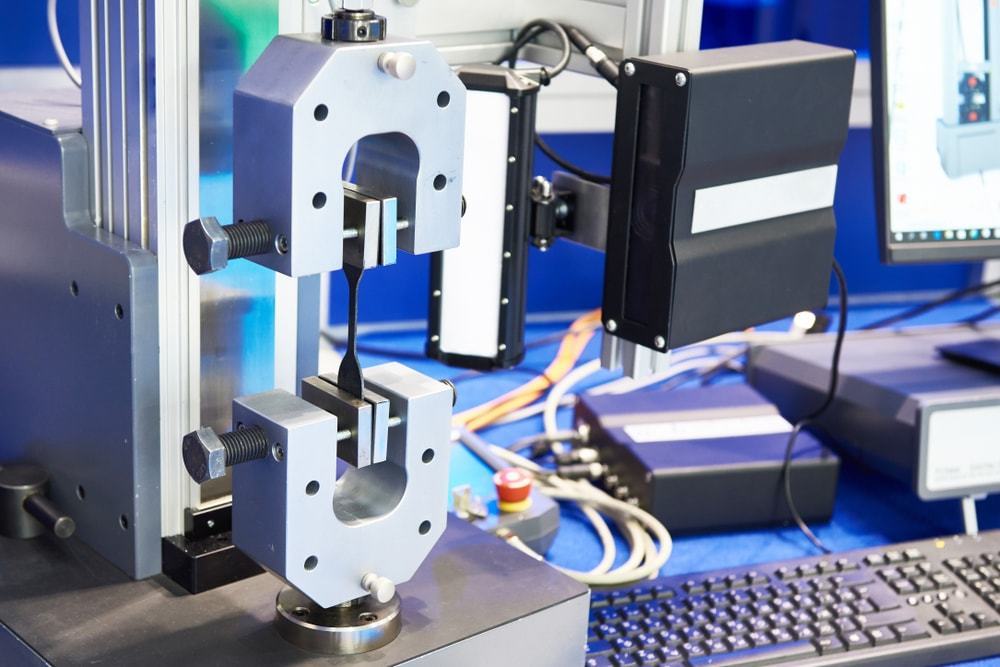
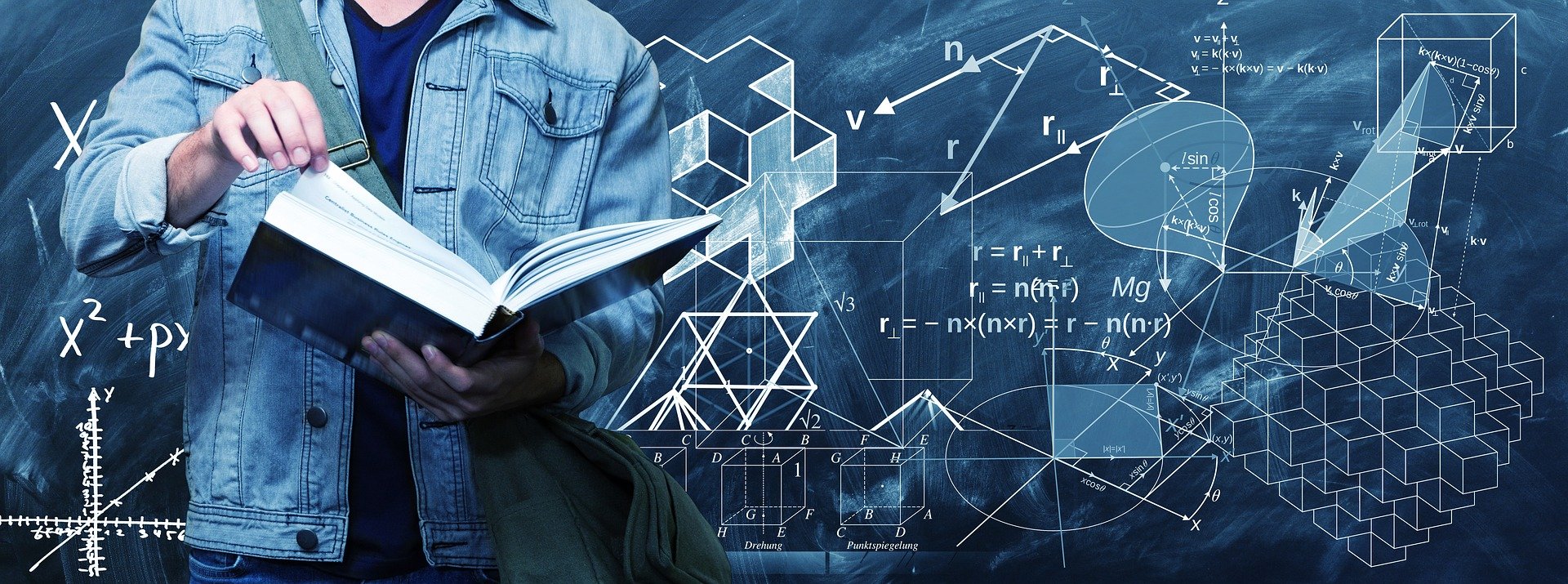
Professional Training Capabilities
Datum offers high-quality online and on-site training on topics like design and engineering, composite processing, inspection and non-destructive testing, material testing, occupational health and safety, and product safety. Datum uses
- It’s primary manufacturing facility for providing on-site theoretical and practical training to aspirants.
- Also, due to our agility we provide the on-site training at our customer’s premises as well.
- Fully-integrated, purposely built Learning Management System (LMS) to host online courses.
All our courses are prepared by world-leading scientists, engineers and industry-experts who have affiliations from GE Aviation, Rolls-Royce, Boeing, Lockheed Martin, Imperial College London, University of Bristol, University of Sheffield, Queen’s University of Belfast and Swansea University.
More information on our professional training courses can be found here.